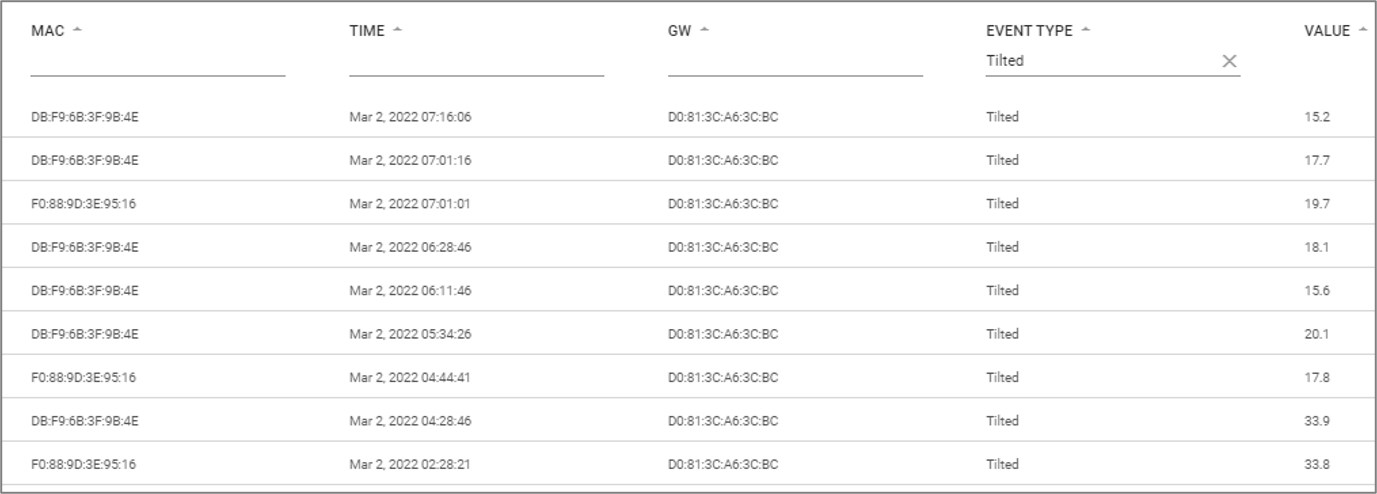
Conveyor Belt Motors
Conveyors are used in almost every step of a mining operation. Atoms paired with Gateways monitor motors all along the line, ensuring continued operation and alerting when a motor's vibration signature changes. Vibration changes and impacts can also be used as a proxy for potential issues with the belt, notifying teams when there are events requiring attention from the operations team. (Note the small AT-C1.0 Atom on the conveyor motor in the picture!)
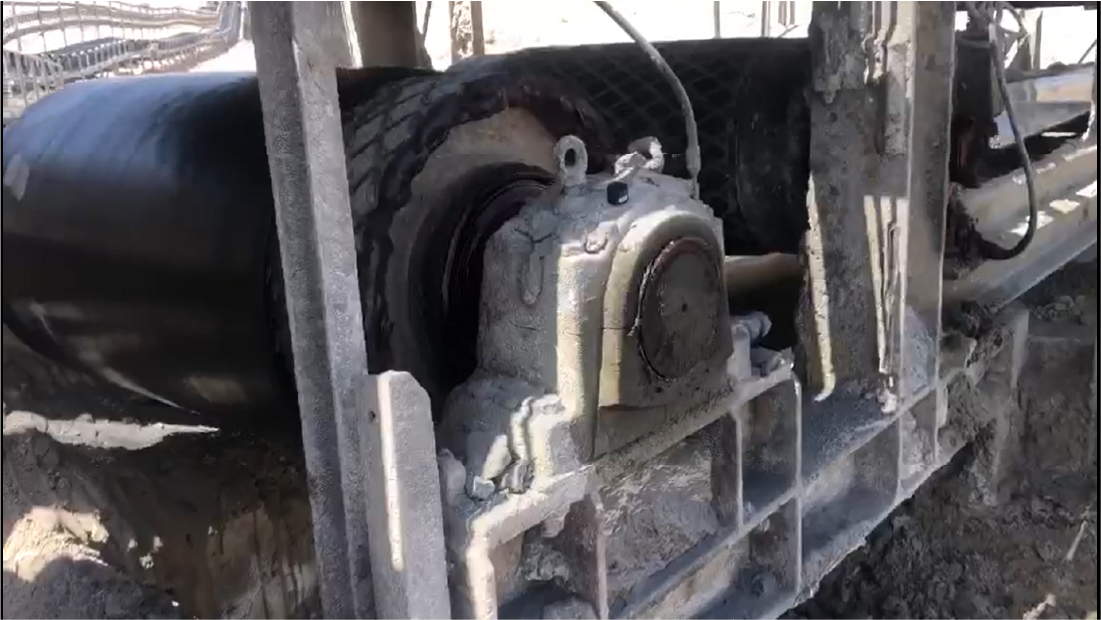
Equipment Maintenance Monitoring
Currently, there is limited information available about the health of the equipment used in a mining operation. Traditionally, equipment performance data has been captured by employees with temperature sensing guns taking periodic readings. This can be problematic for several reasons including variances and inconsistencies in the data captured along with the safety risks associated with capturing temperature on equipment that is difficult to reach or measure. Atoms solve this problem by providing both periodic readings to monitor equipment as well as continuous monitoring for changes in the ongoing operation of a motor or piece of equipment.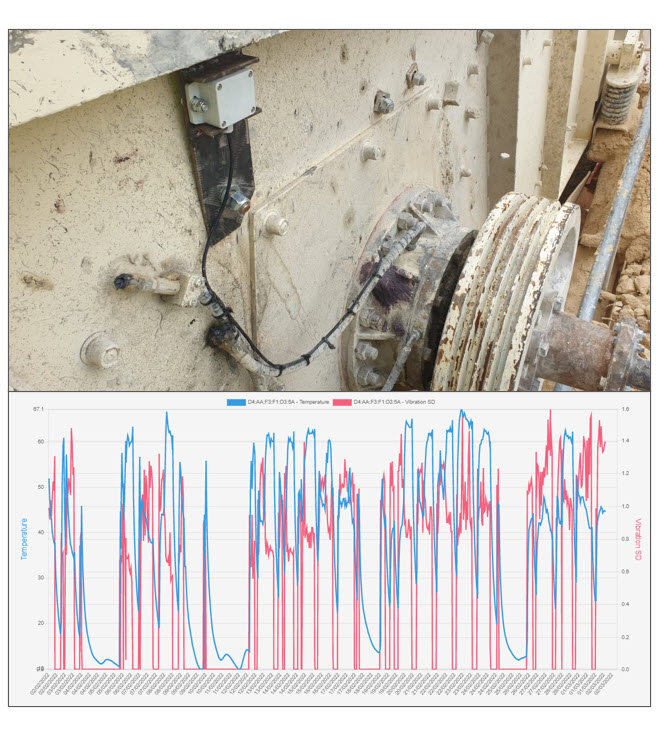
Multiple Atoms are in use in this production step. AT-R1.0 Atoms, connected via Bluetooth to our gateway, are attached to the shaker tables to monitor vibration and impact. An augmented Atom with an external temperature sensor monitors the bearing temperature of the motor. These Atoms provide a detailed view of shaker table performance and deliver alerts when the shakers need attention:
- Bearing Health: bearing temperature increases may signify over-lubrication. Real-time alerts in temperature increase above threshold give operators the opportunity to intervene before failure or damage occurs.
- Screen Health: vibration changes alert operators to screen and motor degradation before the equipment fails, giving operators the opportunity to schedule maintenance, replace critical parts of re-route materials, preventing downtime and equipment failure during operation.
Ports and Shipping
Atoms are back at work in the shipyard, monitoring conveyor motors, shakers and screeners, and crane motors. Because Atoms self-calibrate, install in minutes, and are immediately operational, adding Atoms to each step in the aggregate mining process has proven to be the IoT solution this industry needs.
Delivering on ROI
Another key component of the Atomation platform is the fact that it delivers positive ROI very quickly. The cost of an Atom is significantly lower than the labor costs involved in periodic monitoring. Add that Atoms continuously monitor equipment for issues that may arise, giving teams the opportunity to proactively manage equipment and prevent downtime, and the solution delivers positive ROI almost from day one.
How can Atoms transform your operation? Schedule a demo today and let's work together to see where Atoms can best assist your efforts to improve your operations.
Monitor Equipment in Harsh Environments
With durable and NEMA 6X rated cases, Atoms can be used in places other sensors can't. Check out these additional use cases and then contact us to schedule a demo today.
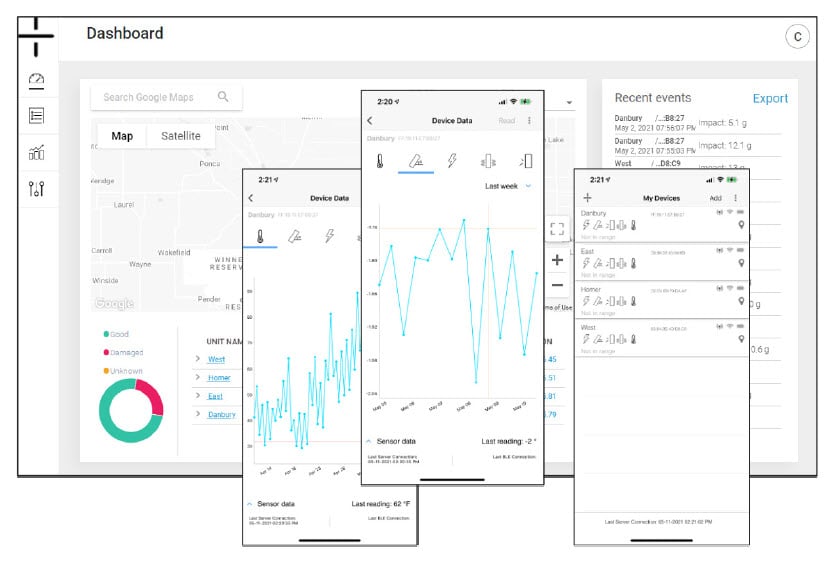